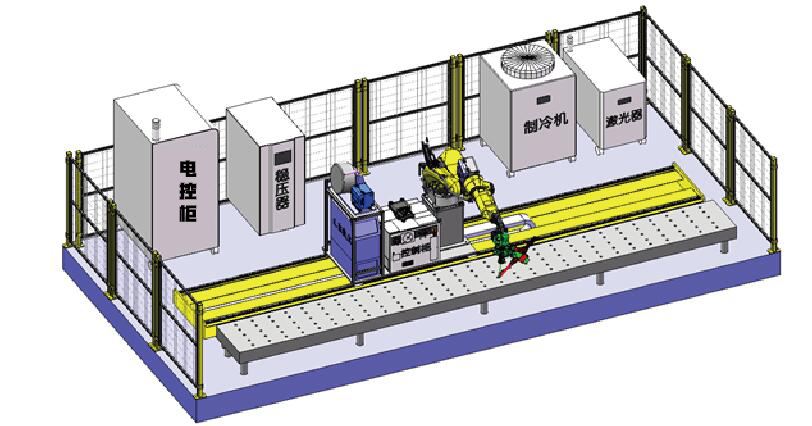
Hybrid welding technology refers to the process of combining laser welding with other welding methods. Compatible processes are MIG (inert gas shielded welding) or MAG (active gas shielded welding) welding, TIG (tungsten inert gas welding) or plasma welding. Hybrid welding technology is faster and has less part deformation than MIG welding alone.
Pure laser welding has the characteristics of high energy density, high welding efficiency, small deformation after welding, narrow heat affected zone and no contact with the workpiece.
Pure laser welding also has the following shortcomings:
① The laser spot diameter is small and the assembly requirements (gap, misalignment, unequal thickness, etc.) are high.
② The base material is partially melted or vaporized by laser heating and then quickly solidifies to form a keyhole. The gas in the hole is difficult to escape, resulting in defects such as pores and shrinkage.
③ Laser photo-induced plasma absorbs, reflects and refracts laser energy, thereby reducing the laser absorption rate, utilization rate and energy conversion rate.
④ Low melting point alloy elements are easy to burn. ⑤ Equipment and maintenance costs are high [3]. Therefore, this limits the application of pure laser welding to a certain extent.
Due to the synergistic effect of laser and other heat sources, the pinhole characteristics and heat source distribution of the laser are changed, the macroscopic morphology of the weld is optimized, the microstructure and mechanical properties are improved, which not only effectively compensates for the shortcomings of pure laser welding, but also achieves the welding effect of “1+1>2”. Therefore, laser composite welding is increasingly widely used in aerospace, automobile, shipbuilding and petrochemical fields.
Working principle of combined laser welding:
Laser composite welding generally refers to the laser welding of two beams in different states (spatial position, beam quality, spot shape, beam energy, light wavelength, action time, etc.) acting on the welding position; the more commonly used method is to coaxially synthesize two beams with different wavelengths and then act on the welding position at the same time.
Central beam: high energy density, small spot area, deep melting welding, providing main welding energy
Peripheral beam: low energy density, large spot area, mainly for preheating, cooling and buffering, improving central beam absorption and auxiliary welding
Fiber laser has small concentrated spot and large energy, which is more suitable for deep melting welding. Blue light has large concentrated spot and small energy, which can preheat the plate and form a certain temperature field, so that the laser energy absorption of the molten pool is more uniform, eliminating welding holes, improving welding quality, improving the absorption rate of fiber laser plate, effectively improving welding efficiency and quality, reducing welding defects, and having better welding adaptability for thin, high reflectivity or high thermal conductivity materials.
.jpg)
Advantages and characteristics of composite welding
The welding surface is smooth and flat, without blackening and yellowing, no cracks, and good sealing
Compared with traditional welding, the speed of composite welding can be increased by 2-3 times;
The processing power used for composite welding is significantly reduced by about 30% compared with simple single-beam fiber continuous welding;
The yield of composite welding is significantly improved;
Pay attention to the use of protective gas during welding;
If there are impurities in the shell, it is easy to produce explosion points, which can be repaired by welding;
The fault tolerance of the welding trajectory of the composite welding is significantly improved compared with that of the single fiber welding.
Functional features:
System composition: industrial robot body, laser, laser head, arc welding machine and welding gun, push-pull wire feeder, laser tracker (optional), movable robot ground rail, refrigerator, voltage stabilizer, electric control cabinet, laser safety guardrail, etc.;
The laser welding software deeply integrated with the robot control system can realize free parameter setting;
It can be equipped with the laser tracking system independently developed by Aotai to realize the positioning function, real-time tracking welding, scanning first and then welding, etc.;
Provide a variety of options (can be customized non-standard), single workstation, ground rail movable workstation, gantry workstation, etc.
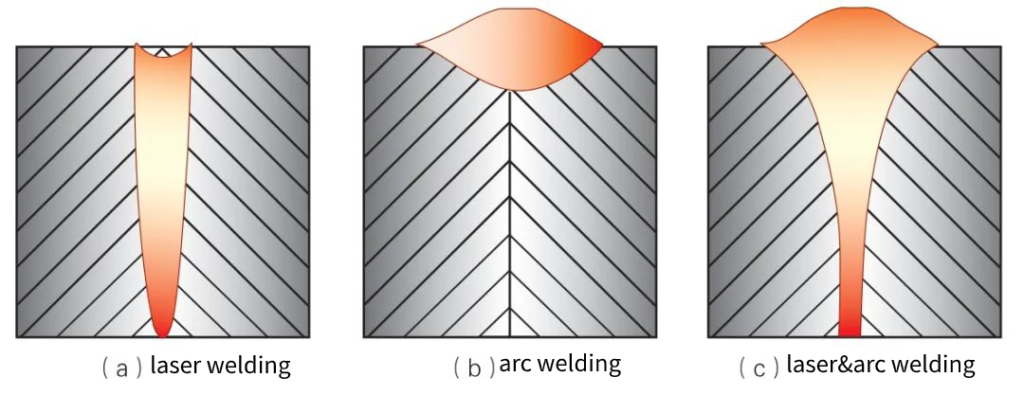
With the continuous development of laser composite welding technology, its application range is becoming more and more extensive. In the welding of thick plates for ships, laser composite welding has greatly improved the welding quality and efficiency. Some foreign shipyards even use laser composite welding methods for ship welding. In the automotive industry, laser composite welding is used for the connection and manufacturing of components such as automobile doors, and can also be used for the connection and manufacturing of power battery trays for new energy vehicles. In the petrochemical industry, laser composite welding improves the welding quality and efficiency of fuel tank welding. In the welding of oil transportation pipelines, the welding process is more stable, the weld is well formed, the weld width ratio is good, there are no welding defects such as undercut and lack of fusion, and the engineering requirements are met. In the aerospace field, laser composite welding is used for the welding of medium and thick plates with high-strength steel, which can greatly reduce the labor intensity of workers and improve welding production efficiency.