industry
Application of Laser Welding Technology in the Field of Metal Processing
Introduction
Laser welding technology has emerged as a groundbreaking innovation in the field of metal processing, revolutionizing the way industries approach the joining of metals. The precision, speed, and versatility of laser welding make it a preferred choice across various sectors. This technology, which involves the use of a laser beam as a concentrated heat source to fuse materials, offers numerous advantages over traditional welding methods.
In this article, we will explore the various applications of laser welding in metal processing, the industries where it is predominantly used, the barriers and challenges associated with its adoption, the functionalities it enables, and a comparison with conventional welding techniques. Additionally, we will recommend some of the best laser welding machines available in the market and conclude with a summary of the key points discussed.
Overview of Laser Welding Technology
Laser welding is a process that utilizes a highly focused laser beam to melt and join metal surfaces. The laser generates a concentrated heat source, allowing for deep penetration and minimal thermal distortion. This method is particularly advantageous for materials that are difficult to weld using traditional techniques, such as high-strength steels, aluminum, and titanium alloys. The process can be automated and controlled with high precision, making it suitable for complex and delicate applications.
Laser welding can be categorized into several types based on the power and wavelength of the laser, including CO2 lasers, fiber lasers, diode lasers, and Nd lasers. Each type has its unique characteristics, making it suitable for specific applications. For instance, fiber lasers are known for their high efficiency and ability to produce a smaller spot size, which is ideal for fine and detailed welding tasks.
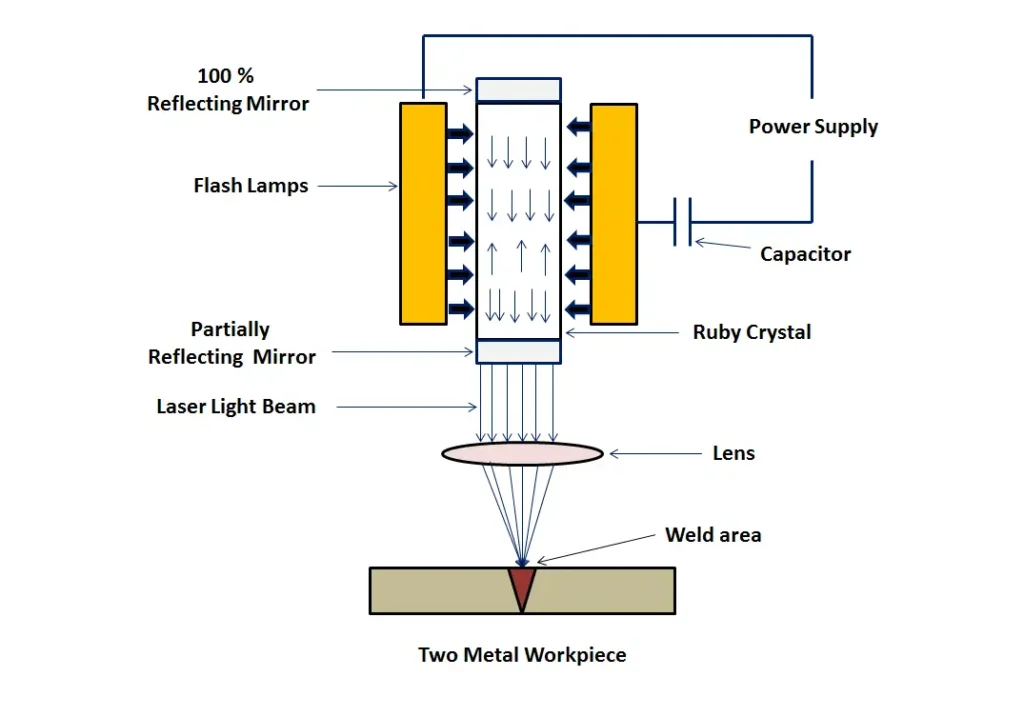
Industries Commonly Using Laser Welding
Automotive Industry
The automotive industry has been one of the early adopters of laser welding technology. This is primarily due to the need for high precision and strong welds in car manufacturing. Laser welding is used for joining various components, including body panels, engine parts, and transmission systems. The ability to produce deep welds with minimal distortion is particularly beneficial for the automotive sector, where safety and durability are paramount.
Aerospace Industry
In the aerospace industry, the demand for lightweight yet strong materials has led to the widespread adoption of laser welding. Components such as turbine blades, fuel tanks, and structural elements of aircraft are often welded using lasers. The technology’s ability to weld dissimilar metals, such as aluminum to titanium, is especially valuable in this industry, where different materials are combined to achieve optimal performance.
Medical Device Manufacturing
The medical device industry requires the fabrication of highly precise and reliable components. Laser welding is used in the production of medical instruments, implants, and devices such as pacemakers. The ability to weld small and intricate parts with high accuracy is crucial in this field, where even minor defects can have serious consequences.
Electronics Industry
In the electronics industry, laser welding is used to join delicate components without causing thermal damage to surrounding areas. This is particularly important in the manufacturing of semiconductors, batteries, and sensors. The precision of laser welding ensures that the electrical properties of the components are not compromised during the welding process.
Jewelry and Watchmaking
The jewelry and watchmaking industries have also embraced laser welding due to its ability to produce clean and precise welds. This is essential for creating intricate designs and repairs on small and delicate items. The non-contact nature of laser welding allows for joining without causing surface damage or discoloration, which is crucial in maintaining the aesthetic quality of the products.
Barriers and Challenges in Laser Welding
Despite its numerous advantages, laser welding faces several barriers and challenges that hinder its widespread adoption:
High Initial Cost
One of the main barriers to the adoption of laser welding technology is the high initial cost of the equipment. Laser welding machines, especially those with high power and advanced features, can be expensive to purchase and maintain. This can be a significant hurdle for small and medium-sized enterprises (SMEs) that may not have the capital to invest in such technology.
Technical Expertise Required
Laser welding requires specialized knowledge and skills to operate the equipment effectively. The setup, programming, and maintenance of laser welding systems can be complex, necessitating trained personnel. The lack of skilled operators can limit the use of laser welding in certain industries.
Material Limitations
While laser welding is highly versatile, it may not be suitable for all materials. Certain metals, such as copper and highly reflective materials, can be challenging to weld using lasers due to their high reflectivity and thermal conductivity. This can lead to inconsistent weld quality and may require additional processing steps or alternative welding methods.
Safety Concerns
The use of high-powered lasers poses safety risks, including the potential for eye injuries and skin burns. Proper safety measures, such as protective eyewear, shielding, and ventilation, are necessary to mitigate these risks. The need for stringent safety protocols can increase the complexity and cost of implementing laser welding technology.
Heat-Affected Zone (HAZ)
Although laser welding minimizes thermal distortion, the heat-affected zone (HAZ) can still be a concern, particularly when welding thin materials or precision components. The HAZ can lead to changes in the material’s microstructure, affecting its mechanical properties and potentially leading to issues such as cracking or reduced strength.
Functional Capabilities of Laser Welding
Laser welding technology offers a range of functionalities that enhance its applicability across various industries:
High Precision and Accuracy
Laser welding allows for precise control over the welding process, enabling the creation of intricate and detailed welds. This is particularly important for applications where tight tolerances are required, such as in the aerospace and medical device industries.
Deep Penetration Welding
Laser welding can achieve deep penetration welds with minimal thermal distortion, making it suitable for thick materials and applications where strength is critical. This capability is especially valuable in industries such as automotive and shipbuilding.
Welding of Dissimilar Metals
Laser welding can be used to join dissimilar metals, such as aluminum to steel or titanium to stainless steel. This is possible due to the localized heating provided by the laser, which reduces the risk of intermetallic formation and ensures a strong bond between the different materials.
Minimal Heat Input
The concentrated heat source of laser welding results in minimal heat input to the surrounding material, reducing the risk of warping, distortion, and damage. This is particularly advantageous for welding thin materials or components that are sensitive to heat.
Automation and Integration
Laser welding systems can be easily automated and integrated into production lines, enhancing efficiency and consistency. The use of robotics and computer control allows for precise and repeatable welds, reducing the need for manual intervention and increasing productivity.
Non-Contact Process
Laser welding is a non-contact process, meaning that the welding tool (the laser beam) does not physically touch the material being welded. This reduces wear and tear on the equipment and minimizes the risk of contamination, making it ideal for cleanroom environments and high-purity applications.
Comparison with Traditional Welding Techniques
Laser welding offers several advantages over traditional welding techniques, but it also has some limitations. Here, we will compare laser welding with common traditional welding methods such as MIG, TIG, and resistance welding:
Advantages of Laser Welding
- Speed: Laser welding is significantly faster than traditional welding methods, allowing for higher throughput and reduced cycle times.
- Precision: The high precision of laser welding enables the creation of fine and detailed welds, which is difficult to achieve with traditional techniques.
- Automation: Laser welding systems are highly compatible with automation, making them ideal for mass production and reducing the need for manual labor.
- Heat Control: The localized heat input of laser welding minimizes the heat-affected zone, reducing the risk of warping and distortion.
- Versatility: Laser welding can be used to weld a wide range of materials, including difficult-to-weld metals and dissimilar materials.
Disadvantages of Laser Welding
- Cost: The high initial cost of laser welding equipment can be a barrier, particularly for smaller businesses.
- Material Limitations: Certain materials, such as highly reflective metals, can be challenging to weld with lasers.
- Technical Complexity: The operation and maintenance of laser welding systems require specialized knowledge and skills, which may not be readily available in all industries.
- Safety Concerns: The use of high-powered lasers requires stringent safety measures to protect operators and prevent accidents.
Comparison with MIG and TIG Welding
- MIG Welding: Metal Inert Gas (MIG) welding is a widely used traditional welding technique that involves the use of a consumable wire electrode and an inert gas to shield the weld area. While MIG welding is relatively simple and cost-effective, it lacks the precision and speed of laser welding. MIG welding is better suited for thick materials and less critical applications, whereas laser welding is preferred for high-precision and high-speed tasks.
- TIG Welding: Tungsten Inert Gas (TIG) welding, also known as Gas Tungsten Arc Welding (GTAW), is another traditional technique that offers high-quality welds with excellent control. However, TIG welding is slower and more labor-intensive compared to laser welding. While TIG welding is ideal for thin materials and applications requiring high weld quality, laser welding offers greater efficiency and precision.
JS-HWG LASER WELDING MACHINE
◆ high quality, high stability, high configuration, high security.
◆ with gas detection alarm, kinetic energy detection, machine minimize loss, to ensure that the machine life;
◆ Additional filters, anti-interference ability, maximize the stability of the machine.
Conclusion
The future of laser welding in the metal processing industry looks promising, with ongoing research and development aimed at further enhancing its capabilities. Innovations such as hybrid laser welding, which combines laser welding with other welding techniques, are being explored to achieve even higher welding speeds and better joint properties. Additionally, advancements in laser sources, such as fiber lasers and diode lasers, are expected to improve the efficiency and versatility of laser welding systems
JNJSINDUSTRY
China Leading Laser Welding Machine Manufacturer
We Follow Best Sevices
JNJSINDUSTRY focus on product quality and customer service
Attitude determines success or failure
- Technology Guidance
- Two-year warranty
- On-site training
- Maintenance guid