INDUSTRY
Applications of Laser Welding in Lithium Battery Assembly
Laser welding: high process barriers, large cylindrical and other new battery technology to pull the welding volume upward
Laser technology with high efficiency and precision, flexible, reliable and stable, small loss of welding consumables, automation and high degree of safety and other characteristics are fully applied to lithium battery cutting, cleaning, welding, marking and other processes. According to the laser manufacturing network official WeChat public number information, in the national policy support and new energy vehicles to promote the application of the process of accelerated drive, China’s automotive power battery demand has grown significantly.
Among the three core components of new energy vehicles, namely battery, motor and electronic control, the core component, lithium power battery, accounts for a high proportion of the cost of the whole vehicle, which also directly determines the range of the whole vehicle. The production of lithium batteries is connected by one process, and the production process is mainly divided into three parts: pole piece manufacturing, core production and battery assembly.
The quality of lithium battery directly determines the performance of new energy vehicles, so the manufacturing process has very high precision requirements. As an advanced “light” manufacturing tool, laser technology, with its high efficiency, precision, flexibility, reliability and stability, low welding material loss, automation and safety, has been applied to cutting, cleaning, welding and marking processes of lithium battery parts.
Laser welding: current status and development prospects
Principle: To ensure battery safety, welding quality depends on laser energy control and process parameters
Laser welding has many advantages such as deep melting, fast speed, small deformation, etc., which can greatly improve the safety of power batteries. According to the prospectus of Lianying Laser, laser welding, as a modern welding technology, has the advantages of deep melting, fast speed, small deformation, low requirements for welding environment, high power density, no influence of magnetic field, not limited to conductive materials, no need for vacuum working conditions, and no X-rays generated during welding.
It is widely used in high-end precision manufacturing, especially in the new energy vehicle and power battery industry. Power batteries have many welding parts, high difficulty, and high precision requirements. Power battery manufacturers also have high requirements for the automation, safety, precision, and processing efficiency of battery production equipment. The unique advantages of laser welding technology can greatly improve the safety, reliability, and consistency of batteries, reduce costs, and extend service life, becoming the best choice for power battery manufacturers.

The main core factors that determine the quality of laser welding are laser energy control and welding process technology. ① Laser energy control: According to the prospectus of Lianying Laser, due to the different absorption rates of the materials being welded to lasers of different wavelengths (ranging from 5% to 50%), different laser selections will result in completely different welding effects.
In order to output a uniform and stable welding laser beam to the weldment, it is necessary to have good consistency in the laser output power or to be able to accurately control the laser output power. Too low power will lead to insufficient welding melting and affect the welding quality. Too high power or fluctuations will lead to spatter, pores and other adverse effects. Therefore, the control of laser energy has become one of the most critical technologies for laser welding.
Welding process technology: According to the prospectus of Lianying Laser, the action process between laser and material is relatively complex. The laser welding effect is related to dozens of factors such as laser wavelength, power density, welding time, welding head angle, focal distance, laser absorption rate and cleanliness of weldment, thickness and thermal conductivity of weldment, shielding gas type and flow rate.
Therefore, laser welding technology is also one of the key factors affecting welding quality. Laser welding technicians need to constantly explore and summarize, and long-term experimental accumulation can achieve good welding results.
According to the working principle, welding can be divided into five types, and different welding methods are selected according to different application requirements to achieve the best effect. According to the prospectus of Lianying Laser, according to different working principles and different processing scenarios, laser welding can be divided into five types: heat conduction welding, deep fusion welding, composite welding, laser brazing and laser conduction welding.
According to different customers and different processing application scenarios, select the appropriate welding method to achieve the best welding effect.
Application status:
Laser welding is used in the production of power batteries in the battery cell manufacturing link and battery PACK link. According to the official website of Lianying Laser, in the production of power batteries, the links using laser welding mainly include: ① Mid-process: welding of pole ears (including pre-welding), spot welding of pole bands, pre-welding of battery cells into shells, sealing welding of outer shell top cover, sealing welding of liquid injection port, etc.; ② Back-end process: including welding of connecting pieces during battery PACK module, and welding of explosion-proof valves on the cover plate behind the module.
Mainly reflected in:
Welding of battery shell and cover plate
Welding of positive and negative poles of battery
Sealing welding of battery explosion-proof valve
Welding of battery adapter
Welding of battery poles
Welding of power battery module and PACK
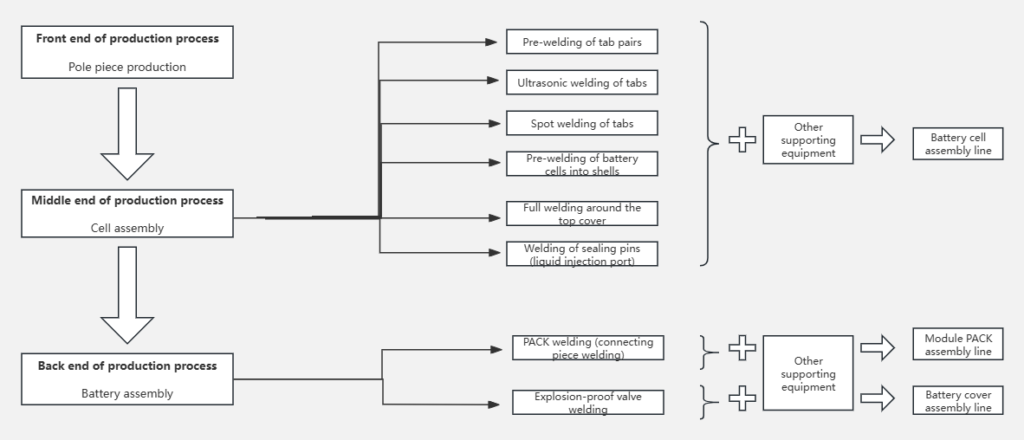
Demand for laser welding machines:
4680 large cylindrical batteries have higher requirements for laser technology, and the welding volume is expected to increase compared to square batteries and small cylindrical batteries. 1) 4680 batteries have higher requirements for laser technology, and the uncontrolled shape of the pole ear is a process difficulty. According to the official website of China Economic Industry Research Institute, the 4680 battery adopts the full-pole ear process, breaking the traditional battery mode of one positive and one negative pole ear.
The process difficulty lies in the uncontrolled shape of the pole ear, which is prone to short circuit. The two sections are closed during manufacturing, and the electrolyte penetration is greatly hindered. In addition, it is difficult to fold the multiple pole ears neatly, which requires higher laser technology. 2) Compared with square batteries and small cylindrical batteries, the laser welding of 4680 large cylindrical batteries has increased the welding process and the required welding equipment.
According to the official website of China Economic Industry Research Institute, 1) compared with square batteries, the laser welding process for the surface welding of the full-electrode ear of large cylindrical batteries has increased from 5 to 7; 2) from the perspective of small cylindrical batteries, 5 welding equipment are added to the production line of single GWh compared with 18650 and 21700 batteries. Combined with the above situation, we believe that the demand for laser welding of 4680 large cylindrical batteries is expected to increase compared with square batteries and small cylindrical batteries.
Problems and prospects of laser welding machines:
Other welding link technologies: Solve the problem of welding dissimilar metals, such as the busbar welding in the battery PACK is expected to be replaced by laser welding. We judge that as the laser welding process continues to improve, the penetration rate of laser welding is expected to increase.
Take the Al/Cu dissimilar metal welding in the busbar welding of the back-end module/PACK of square battery as an example: ① The low light absorption rate of Al and Cu and the easy generation of highly brittle metal compounds are the difficulties of Al/Cu: According to “New Progress in Laser Welding Technology of Al/Cu Dissimilar Metals in Automotive Battery Modules”, due to the different physical properties of Al and Cu, Al/Cu dissimilar metal laser welding has several challenging limitations. One is mainly that the absorption rate of Al is low at a laser wavelength of 1um, while the absorption rate of Cu is even lower; another challenge comes from the metallurgical properties of Al-Cu alloys, that is, highly brittle metal compounds may lead to the formation of cracks.
Intermetallic compound phases with a Cu content of 50%-80% may be formed. Therefore, copper and copper, aluminum and aluminum are generally welded by laser. At the same time, since copper and aluminum have fast heat transfer and high laser reflectivity, the thickness of the connecting sheet is relatively large, so a higher power laser is required to achieve welding. Through various realistic data, we believe that with the continuous advancement of laser technology in the future, busbar Al/Cu laser welding, laser welding is the most likely direction.
Advantages of laser welding:
Energy concentration, high welding efficiency, high processing accuracy, and large weld depth-to-width ratio. The laser beam is easy to focus, align and guide by optical instruments. It can be placed at an appropriate distance from the workpiece and can be guided between fixtures or obstacles around the workpiece. Other welding methods cannot be used due to the above-mentioned space limitations. Small heat input, small heat-affected zone, small residual stress and deformation of the workpiece; welding energy can be precisely controlled, welding effect is stable, and welding appearance is good; non-contact welding, optical fiber transmission, good accessibility, and high degree of automation. When welding thin materials or thin-diameter wires, there will be no trouble of remelting like arc welding.
The battery cells used for power batteries usually use “lighter” aluminum materials due to the principle of “lightness”, and they also need to be made “thinner”. Generally, the shell, cover, and bottom are basically required to be less than 1.0 mm. The current thickness of the basic materials of mainstream manufacturers is about 0.8 mm. It can provide high-strength welding for various material combinations, especially when welding copper materials to aluminum materials. This is also the only technology that can weld electroplated nickel to copper materials.
Benfits of js product:
Precision and Control:Laser welding offers high precision and control over the welding process, which is essential for the delicate and complex structures of lithium batteries. This precision reduces the risk of damaging sensitive components.
Speed and Efficiency:The process is significantly faster than traditional welding methods. This high-speed operation increases production rates and reduces manufacturing costs.
Quality and Consistency:Laser welding provides consistent and repeatable welds with minimal defects. This consistency is crucial for maintaining the high quality standards required in battery production.
Reduced Heat Affected Zone (HAZ):The localized heating of laser welding minimizes the heat-affected zone, reducing the risk of thermal damage to adjacent components and improving the overall reliability of the welds.
Minimal Material Distortion:Due to the precise and localized nature of the laser beam, there is minimal distortion of the materials being welded, which is critical for maintaining the integrity and performance of the battery cells.
Product recommendations:
JS-HWG is a compact and versatile laser welding machine ideal for electronic component manufacturing. It offers high precision, safety and stability. Its user-friendly interface and advanced features make it suitable for both small and large-scale production.
JS-HWN LASER WELDING MACHINE
offers several advantages, including enhanced portability, flexibility, and ease of use. These machines allow operators to perform precise welds in hard-to-reach or constrained spaces, making them ideal for on-site repairs and maintenance. Their lightweight design and ergonomic features reduce operator fatigue and improve productivity. Additionally, handheld welding machines often come with user-friendly interfaces and adjustable settings, enabling quick adjustments and fine-tuning for various welding tasks.
Conclusion:
The adoption of laser welding in lithium battery manufacturing offers significant advantages, including high precision, efficiency, and quality. It is particularly beneficial in applications requiring delicate and complex welds, such as tab welding, cell case sealing, and busbar welding. By reducing the heat-affected zone and being compatible with automation, laser welding improves the overall production process, leading to better performance and reliability of lithium batteries. As the demand for lithium batteries grows, especially in electric vehicles and portable electronics, the use of laser welding technology is likely to become even more prevalent.
JNJSINDUSTRY
China Leading Laser Welding Machine Manufacturer
We Follow Best Sevices
JNJSINDUSTRY focus on product quality and customer service
Attitude determines success or failure
- Technology Guidance
- Two-year warranty
- On-site training
- Maintenance guid