.jpg)
Selecting the appropriate power level for a laser welding machine is a critical decision that significantly influences the quality, efficiency, and overall success of the welding process. The power of the laser is directly related to its ability to penetrate materials, the speed of welding, and the quality of the weld. However, choosing the right power level is not a straightforward task; it requires a deep understanding of various factors, including material properties, thickness, desired weld characteristics, and the specific application needs.
This comprehensive guide explores the factors that determine the appropriate power for a laser welding machine, the different types of lasers available, and how to balance power with other critical parameters to achieve optimal results. By the end of this article, you will have a thorough understanding of how to select the right laser power for your specific welding needs.
Chapter 1: Understanding Laser Power in Welding
1.1. Definition of Laser Power
Laser power refers to the amount of energy that the laser source emits, typically measured in watts (W) or kilowatts (kW). In the context of laser welding, power is a crucial factor that determines how effectively the laser can melt and join materials.
- Continuous Wave (CW) Power: Refers to the average power output of the laser when it is operated continuously. This is most common in high-power industrial lasers.
- Pulsed Power: Some lasers operate in pulses rather than a continuous beam. In this case, the peak power during each pulse can be much higher than the average power, making it suitable for precision welding of delicate materials.
1.2. The Role of Power in Welding Quality
The power of the laser affects several key aspects of the welding process:
- Penetration Depth: Higher power levels allow the laser to penetrate deeper into the material, enabling the welding of thicker sections.
- Weld Speed: Increased power allows for faster welding speeds, reducing cycle times and increasing productivity.
- Heat Affected Zone (HAZ): The amount of power and how it’s applied can affect the size of the HAZ, which impacts the surrounding material’s properties.
- Weld Consistency: Adequate power ensures consistent weld quality, reducing the likelihood of defects such as cracks, porosity, or incomplete fusion.
Chapter 2: Factors to Consider When Choosing Laser Power
2.1. Material Properties
Different materials absorb and react to laser energy differently, which influences the required laser power.
- Reflectivity: Highly reflective materials like aluminum or copper require higher power to achieve effective absorption because they reflect much of the laser energy away.
- Thermal Conductivity: Materials with high thermal conductivity, such as copper, dissipate heat quickly, necessitating higher power to maintain the necessary temperature for welding.
- Melting Point: Materials with a higher melting point require more power to reach the temperature needed for welding.
2.2. Material Thickness
The thickness of the material being welded is a primary factor in determining the required laser power. Thicker materials require more energy to melt through the entire cross-section.
- Thin Materials: For materials with a thickness of less than 1 mm, lower power lasers (in the range of 1KW) are typically sufficient.
- Medium Thickness Materials: For materials between 1 mm and 3 mm, medium power lasers (1KW to 2 kW) are often used.
- Thick Materials: Materials thicker than 3 mm generally require high-power lasers (above 2 kW) to achieve proper penetration and weld quality.
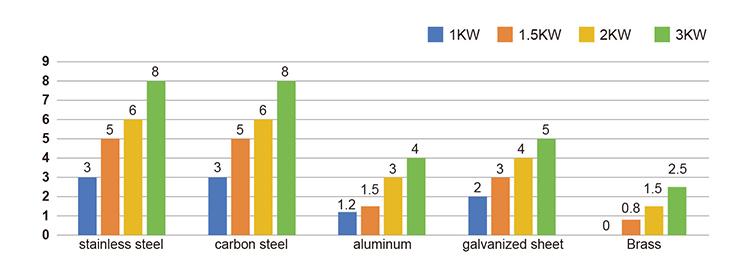
2.3. Welding Speed
The speed at which the welding process occurs also affects the choice of power. Higher power allows for faster welding, which is desirable in high-volume production environments.
- High-Speed Welding: In situations where speed is critical, such as in automotive manufacturing, higher power lasers (e.g., 4 kW and above) are used to maintain productivity without compromising weld quality.
- Low-Speed Welding: For applications where precision is more important than speed, such as in the medical device industry, lower power lasers (under 1 kW) are often sufficient.
2.4. Joint Design and Accessibility
The design of the joint and the accessibility of the welding area also influence the required laser power.
- Butt Joints: These joints typically require less power compared to lap joints because the laser only needs to penetrate through the thickness of one material.
- Lap Joints: These joints require more power as the laser must penetrate through the overlapping materials to form a strong weld.
- T-Joints and Corner Joints: The complexity of these joints may necessitate higher power to ensure that the laser reaches all areas effectively.
2.5. Desired Weld Quality
The desired characteristics of the weld also play a role in power selection.
- Aesthetic Welds: For applications where the visual appearance of the weld is critical, such as in jewelry or consumer electronics, lower power with high control is often preferred to create clean, smooth welds.
- Structural Welds: In applications where the strength and integrity of the weld are paramount, such as in construction or aerospace, higher power is required to ensure deep penetration and strong bonds.
2.6. Type of Laser Source
Different laser sources have varying efficiencies and capabilities, which affect the power required.
- CO2 Lasers: These are often used for welding thicker materials due to their higher power capabilities, typically ranging from 1 kW to 20 kW.
- Fiber Lasers: Fiber lasers are more efficient and can achieve high power densities with lower overall power. They are commonly used for precision welding applications.
- Diode Lasers: Diode lasers are suitable for low to medium power applications and are often used in welding plastics or thin metals.
Chapter 3: Balancing Power with Other Welding Parameters
3.1. Power Density and Focal Spot Size
Power density is the amount of power per unit area and is determined by the laser power and the focal spot size.
- Smaller Focal Spot: Concentrating the laser power into a smaller spot increases the power density, allowing for more precise welding. This is ideal for fine detail work.
- Larger Focal Spot: A larger focal spot spreads the power over a wider area, which can be beneficial for welding larger components or when deep penetration is required.
3.2. Pulse Frequency and Duration
In pulsed laser welding, the pulse frequency and duration also influence the required power.
- High Pulse Frequency: Higher frequencies can increase the average power delivered to the workpiece, which is useful for faster welding.
- Pulse Duration: Shorter pulses deliver more power in a shorter time, which can be beneficial for reducing the heat-affected zone and preventing thermal damage to sensitive components.
3.3. Welding Speed and Power Balance
The relationship between welding speed and laser power is critical. Increasing the welding speed typically requires more power to maintain the same penetration depth and weld quality.
- High Speed, High Power: In high-speed applications, using a higher power laser ensures that the material melts sufficiently despite the rapid movement.
- Low Speed, Low Power: For precision applications, slower speeds and lower power allow for greater control over the weld and reduce the risk of defects.
3.4. Heat Input Management
Managing heat input is essential to avoid issues such as warping, excessive melting, or an overly large heat-affected zone.
- Controlled Heat Input: By carefully selecting the laser power, pulse frequency, and speed, you can manage the heat input to achieve the desired weld characteristics.
- Cooling and Shielding: Using shielding gases and cooling systems can help manage the heat input and protect the weld from oxidation and contamination.
Chapter 4: Challenges and Solutions in Power Selection
4.1. Overcoming Reflectivity Issues
Highly reflective materials like copper and aluminum can pose challenges in laser welding.
- Solution: Increasing the power of the laser and using shorter wavelengths (e.g., with a fiber laser) can enhance absorption and improve weld quality.
4.2. Managing Thermal Distortion
Excessive power can lead to thermal distortion, especially in thin materials.
- Solution: Carefully balancing power with welding speed and using pulsed laser techniques can minimize heat input and reduce the risk of warping.
4.3. Achieving Consistent Weld Quality
Inconsistent power delivery can result in variable weld quality.
- Solution: Using advanced control systems and real-time monitoring can help maintain consistent power levels and ensure uniform welds.
4.4. Addressing Cost Considerations
Higher power lasers are more expensive, both in terms of initial investment and operational costs.
- Solution: Assess the specific needs of the application and consider whether a lower power laser, with optimized parameters, can achieve the desired results more cost-effectively.
Conclusion
Choosing the right power for a laser welding machine is a complex but crucial task that directly impacts the success of the welding process. By considering factors such as material properties, thickness, welding speed, and desired weld quality, you can make an informed decision that balances power with other critical parameters. Whether you are in the automotive, aerospace, medical, electronics, or jewelry industry, understanding how to select the appropriate laser power will help you achieve optimal welding performance, ensuring both efficiency and quality in your manufacturing processes.
As laser technology continues to evolve, further advancements in power management, efficiency, and precision are expected, making laser welding an even more versatile and powerful tool in modern manufacturing.