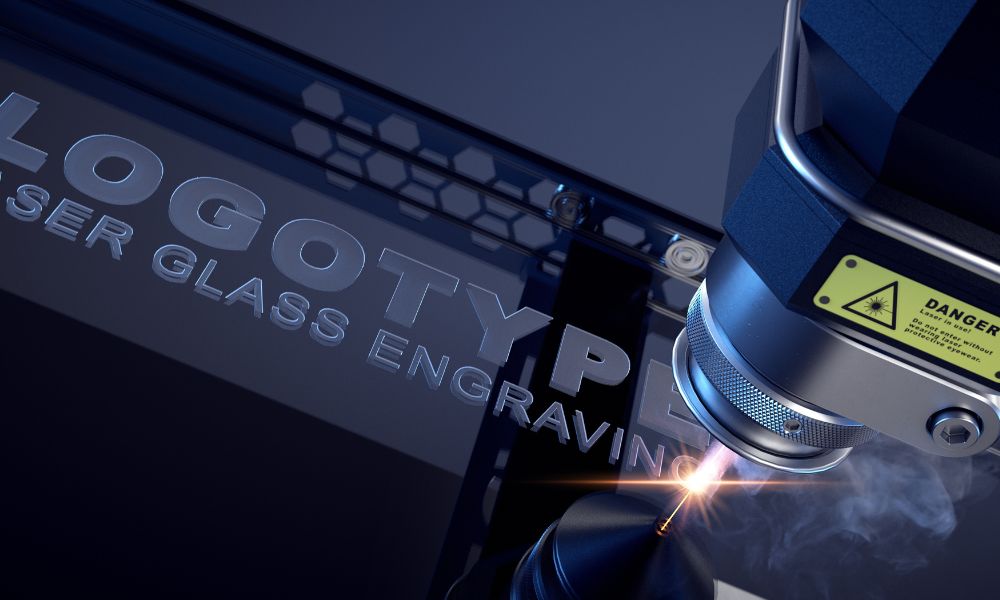
Laser marking technology has become an essential tool in various industries, offering precision, speed, and versatility for marking materials ranging from metals and plastics to ceramics and glass. Whether you’re in manufacturing, automotive, electronics, or even the medical field, choosing the right laser marking technology is crucial for achieving optimal results. This article will explore the different types of laser marking technologies, the factors to consider when choosing the right one, and how to align your selection with your specific application needs.
1. Overview of Laser Marking Technologies
Laser marking involves using a focused beam of light to create a permanent mark on the surface of a material. There are several laser marking technologies, each with its strengths and ideal applications. Understanding these technologies is the first step in choosing the right one.
1.1. Fiber Laser Marking
Fiber laser marking technology is one of the most popular and widely used methods due to its versatility and efficiency. It operates by using a fiber optic cable to amplify light and produce a high-intensity beam that can mark a variety of materials.
- Applications: Fiber lasers are ideal for marking metals (such as stainless steel, aluminum, and copper), plastics, and some ceramics. They are commonly used in industries like automotive, aerospace, electronics, and medical devices.
- Advantages: Fiber lasers offer high precision, fast marking speeds, and low maintenance. They also have a long operational life and can produce high-contrast marks, making them suitable for applications requiring detailed and durable markings.
1.2. CO2 Laser Marking
CO2 lasers are gas lasers that use a gas mixture (typically carbon dioxide, nitrogen, and helium) to generate the laser beam. CO2 lasers are particularly effective for marking non-metallic materials.
- Applications: CO2 laser marking is best suited for organic materials such as wood, leather, paper, glass, textiles, and certain plastics. It is widely used in packaging, labeling, and engraving industries.
- Advantages: CO2 lasers are known for their ability to mark a wide range of non-metals with precision and speed. They can engrave or mark with varying depths, making them versatile for both surface marking and deep engraving applications.
1.3. UV Laser Marking
Ultraviolet (UV) laser marking technology operates at a shorter wavelength compared to fiber and CO2 lasers, allowing for cold marking processes. This means the material’s surface is marked with minimal heat, reducing the risk of damage.
- Applications: UV lasers are suitable for marking materials that are sensitive to heat, such as plastics, glass, ceramics, and certain metals. They are often used in the medical, electronics, and pharmaceutical industries.
- Advantages: UV lasers produce high-precision, high-contrast marks with minimal thermal impact on the material. This makes them ideal for marking delicate materials or components that require clean and fine detailing.
1.4. Green Laser Marking
Green laser marking uses a wavelength of 532 nm, making it effective for marking highly reflective materials and materials that are difficult to mark with other laser types.
- Applications: Green lasers are commonly used for marking metals, semiconductors, glass, and some plastics. They are particularly useful for marking electronic components, solar cells, and medical devices.
- Advantages: Green lasers offer high precision and can mark reflective surfaces without causing damage or requiring additional surface preparation. They are also effective for marking transparent materials like glass.
1.5. MOPA Laser Marking
MOPA (Master Oscillator Power Amplifier) lasers are a type of fiber laser that offers adjustable pulse durations, providing more flexibility in the marking process.
- Applications: MOPA lasers are versatile and can mark a wide range of materials, including metals, plastics, and coated surfaces. They are often used in industries requiring high-quality markings, such as electronics, automotive, and aerospace.
- Advantages: The adjustable pulse duration of MOPA lasers allows for more control over the marking process, enabling the creation of high-contrast marks, color markings on metals, and precise engraving on delicate materials.
2. Factors to Consider When Choosing Laser Marking Technology
Choosing the right laser marking technology requires careful consideration of several factors, including the material being marked, the type of mark required, production speed, and budget. Below are key factors to guide your decision.
2.1. Material Type
The material you need to mark plays a significant role in determining the appropriate laser technology. Different lasers interact with materials in unique ways, affecting the quality and durability of the mark.
- Metals: Fiber lasers are typically the best choice for metals due to their high power and precision. For reflective metals like copper or aluminum, green lasers might be more suitable.
- Plastics: UV and fiber lasers are both effective for marking plastics, but the choice depends on the specific type of plastic and the desired mark. UV lasers are preferred for heat-sensitive plastics to avoid material damage.
- Organic Materials: CO2 lasers excel in marking organic materials like wood, leather, and textiles. Their ability to cut and engrave non-metals makes them versatile for various applications.
- Glass and Ceramics: UV and green lasers are ideal for marking glass and ceramics due to their ability to produce fine, detailed marks without causing cracks or damage.
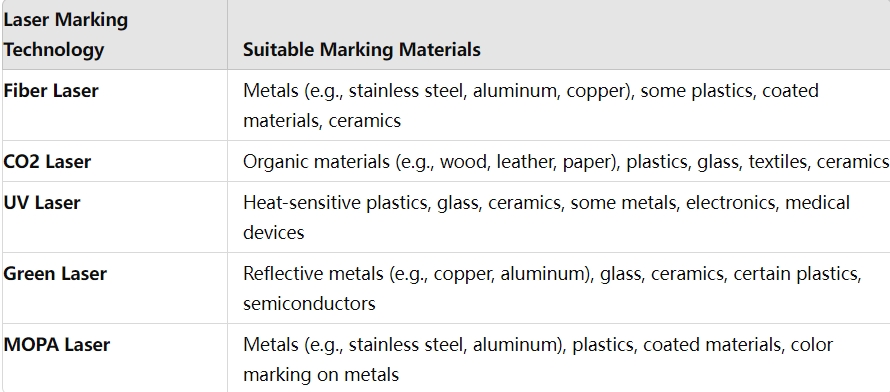
2.2. Marking Requirements
Understanding the type of mark you need to achieve is crucial. Consider whether you need surface marking, deep engraving, color marking, or high-contrast marking.
- Surface Marking: For shallow, surface-level marks, fiber or CO2 lasers are typically sufficient. These marks are often used for logos, barcodes, and serial numbers.
- Deep Engraving: Deep engraving requires higher power lasers, such as fiber or CO2 lasers, that can penetrate the material surface without compromising quality.
- Color Marking: If color marking on metals is required, a MOPA laser with adjustable pulse durations is the best choice. This capability is particularly useful in branding and product customization.
- High-Contrast Marking: For applications requiring high contrast, such as in medical devices or electronics, UV lasers are preferred due to their ability to produce sharp, clean marks with minimal thermal impact.
2.3. Production Speed
The speed of the marking process is another critical factor, especially in high-volume production environments. The laser’s marking speed can impact overall productivity and operational efficiency.
- High-Speed Production: Fiber and CO2 lasers are known for their high marking speeds, making them ideal for industries where quick turnaround times are essential, such as in packaging and labeling.
- Batch Production: If your production involves batch processing, ensure the laser marking system can handle multiple items simultaneously without sacrificing quality or speed.
2.4. Marking Area Size
The size of the marking area required for your application can influence your choice of laser. Some lasers are better suited for large marking areas, while others excel in precision marking on smaller areas.
- Large Marking Areas: For applications requiring large marking areas, such as in signage or large metal sheets, a CO2 laser or a fiber laser with a large working area is suitable.
- Small, Detailed Marking: For small, intricate marks, such as those on jewelry, electronic components, or medical devices, UV or green lasers are ideal due to their high precision and fine beam control.
2.5. Environmental Considerations
Consider the environment in which the laser marking system will be used. Factors such as temperature, humidity, and dust can affect the performance and longevity of the equipment.
- Cleanroom Environments: In industries like pharmaceuticals or electronics, where cleanroom conditions are necessary, UV or green lasers are often preferred due to their ability to operate in controlled environments.
- Harsh Industrial Environments: For environments with high levels of dust or temperature fluctuations, fiber lasers are generally more robust and can withstand tougher conditions.
2.6. Budget Constraints
The cost of the laser marking system, including initial investment, maintenance, and operational costs, is a significant factor in the decision-making process.
- Initial Investment: CO2 lasers are generally more affordable than fiber lasers, making them a cost-effective option for small businesses or applications with lower precision requirements.
- Long-Term Costs: Consider the long-term operational costs, including maintenance, energy consumption, and consumables. Fiber lasers, while more expensive initially, often have lower maintenance costs and longer operational life.
2.7. Regulatory and Compliance Requirements
Certain industries, such as medical devices, aerospace, and automotive, have strict regulatory requirements for marking and traceability. Ensure that the chosen laser marking technology meets these standards.
- Traceability: For industries requiring traceability, such as medical devices, the ability to produce clear, durable, and permanent marks is essential. Fiber and UV lasers are often preferred for their precision and reliability.
- Compliance: Verify that the laser marking system complies with industry-specific regulations, such as FDA or CE marking requirements, to avoid legal and operational issues.
3. Aligning Laser Marking Technology with Industry Applications
Different industries have specific needs when it comes to laser marking. Below, we explore how various industries can align their applications with the appropriate laser marking technology.
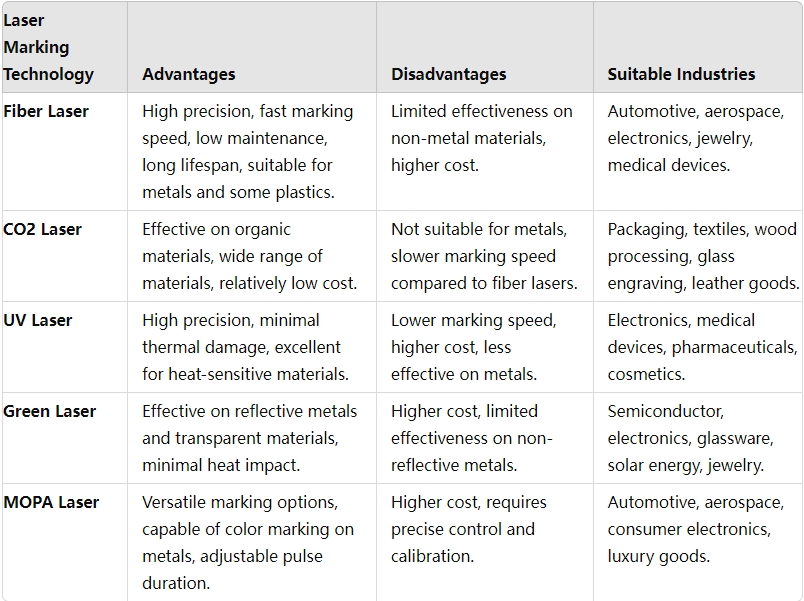
4. Implementation and Integration of Laser Marking Systems
Once the appropriate laser marking technology has been selected, the next step is to integrate it into your production process. Proper implementation ensures that you maximize the benefits of the technology.
4.1. System Integration
Integrating the laser marking system into your existing production line requires careful planning to ensure compatibility, efficiency, and minimal disruption.
- Automation: Consider integrating the laser marking system with automated processes, such as robotic arms or conveyor systems, to improve efficiency and throughput.
- Software Compatibility: Ensure that the laser marking system is compatible with your existing software for design, coding, and database management to streamline the marking process.
4.2. Operator Training
Proper training for operators is essential to ensure that the laser marking system is used safely and effectively.
- Safety Protocols: Train operators on safety protocols, including the use of protective equipment and proper handling of the laser system.
- System Operation: Provide comprehensive training on system operation, including setting parameters, maintenance, and troubleshooting.
4.3. Maintenance and Support
Regular maintenance is crucial to ensure the longevity and optimal performance of the laser marking system.
- Scheduled Maintenance: Establish a maintenance schedule to inspect and service the laser system, including cleaning optics, checking alignment, and replacing consumables.
- Technical Support: Choose a supplier that offers robust technical support and service agreements to address any issues that may arise.
4.4. Cost Considerations
Evaluate the total cost of ownership, including initial investment, operational costs, and maintenance expenses.
- Budget Planning: Plan your budget to include not only the purchase price but also ongoing costs such as maintenance, energy consumption, and potential upgrades.
- Return on Investment (ROI): Calculate the ROI by considering the increased efficiency, reduced waste, and improved quality that the laser marking system will bring to your production process.
Conclusion
Choosing the right laser marking technology involves a detailed understanding of your specific application needs, material properties, and production requirements. By considering factors such as material type, marking requirements, production speed, and budget, you can make an informed decision that will enhance your manufacturing processes and product quality. Laser marking technology continues to evolve, offering increasingly sophisticated solutions that meet the demands of various industries. By carefully selecting and implementing the right laser marking system, you can ensure long-term success and stay competitive in your industry.