Industry
Application of laser welders in automobile manufacturing industry
Laser welding technology is mainly used for welding of unequal thickness plates and body welding. Laser welding is mainly used for welding of body frame structure, such as welding of top cover and side panel.
Laser welding is applied to automobiles to reduce the weight of the body and thus save fuel; improve the assembly accuracy of the body and increase the body rigidity by 30%, thereby improving the safety of the body; reduce the stamping and assembly costs in the manufacturing process of the automobile body, reduce the number of body parts, and improve the degree of body integration.
Since the 1980s, laser welding technology has been applied to the field of automobile body manufacturing, mainly for laser welding of body. Laser technology uses a polarizer to reflect the beam generated by the laser to concentrate it in the focusing device to generate a beam of huge energy, so that the workpiece melts instantly, thereby realizing the welding process.
Current application status of laser welding machines in the automotive industry:
Car body welding
Most of the laser welding in the automotive industry is used in the assembly and connection of stamped parts of the car body, mainly including the laser welding of the roof cover, trunk cover and frame. Another important one is the laser welding of the car body, which is about the structural parts of the car body, including doors, body side frames and pillars.
The use of laser welding can improve the strength of the car body and solve the problem of conventional resistance spot welding. For the composite welding of the overall internal structure of a car body structure, such as the overall welding of the vehicle roof and the body chassis, new technologies such as micro laser overall welding are used to improve the welding rigidity of the overall body structure of the vehicle, make the body more integrated, and reduce production costs.
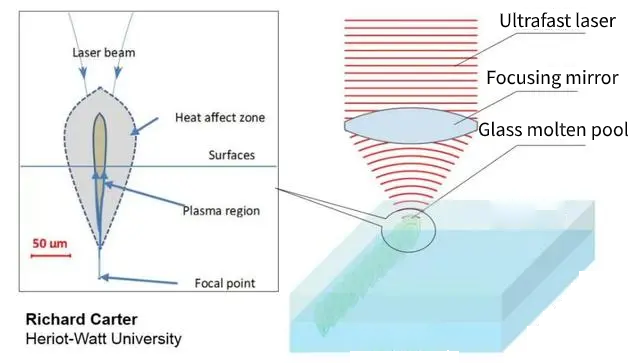
Uniform thickness laser welded plates
Using unequal thickness laser welded plates in car body manufacturing can reduce the weight of the car body, reduce the number of parts, improve safety and reliability, and reduce production costs, but this requires extremely high welding technology.
Gear and transmission parts welding
In addition, various parts of the gearbox can be welded on this equipment, especially the differential case and drive shaft in the car gearbox, which are often produced by individual parts and then joined and welded together.
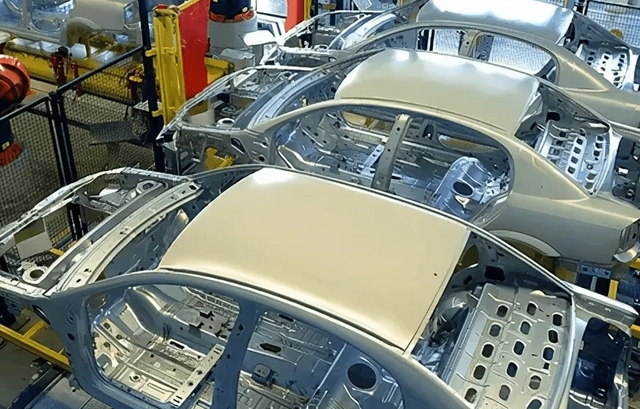
Principle of laser welding:
Laser welding can be realized by continuous or pulsed laser beam. The principle of laser welding can be divided into heat conduction welding and laser deep penetration welding. Our application in the automotive industry is mainly laser deep penetration welding. Laser deep penetration welding generally uses a continuous laser beam to complete the connection of materials.
Its metallurgical physical process is very similar to electron beam welding, that is, the energy conversion mechanism is completed through the “key-hole” structure. Under the irradiation of laser with sufficiently high power density, the material evaporates and forms a key hole. This key hole filled with steam is like a black body, absorbing almost all the energy of the incident beam. The equilibrium temperature in the cavity is about 2500 0C. Heat is transferred from the outer wall of this high-temperature cavity to melt the metal surrounding the cavity.
The key hole is filled with high-temperature steam generated by the continuous evaporation of the wall material under the irradiation of the beam. The four walls of the key hole are surrounded by molten metal, and the liquid metal is surrounded by solid materials (in most conventional welding processes and laser conduction welding, the energy is first deposited on the surface of the workpiece and then transferred to the inside).
The liquid flow outside the hole wall and the surface tension of the wall layer are in a dynamic balance with the steam pressure continuously generated in the hole cavity. The light beam continuously enters the small hole, and the material outside the small hole is continuously flowing. As the light beam moves, the small hole is always in a stable state of flow. That is to say, the small hole and the molten metal surrounding the hole wall move forward with the forward speed of the leading light beam. The molten metal fills the gap left after the small hole is removed and condenses, and the weld is formed.
Its main process parameters:
Laser power. There is a laser energy density threshold in laser welding. Below this value, the penetration depth is very shallow. Once it reaches or exceeds this value, the penetration depth will increase significantly. Only when the laser power density on the workpiece exceeds the threshold (related to the material), plasma will be generated, which indicates that stable deep penetration welding is carried out.
If the laser power is lower than this threshold, only the surface of the workpiece melts, that is, the welding is carried out in a stable heat conduction type. When the laser power density is near the critical condition for the formation of the small hole, deep penetration welding and conduction welding are carried out alternately, becoming an unstable welding process, resulting in large fluctuations in penetration depth. During laser deep penetration welding, the laser power controls both the penetration depth and the welding speed.
The penetration depth of welding is directly related to the beam power density and is a function of the incident beam power and the beam focal spot. Generally speaking, for a laser beam of a certain diameter, the penetration depth increases as the beam power increases.
Beam focal spot. The beam spot size is one of the most important variables in laser welding because it determines the power density. However, for high-power lasers, its measurement is a difficult problem, although there are many indirect measurement techniques.
Material absorption value. The absorption of laser by the material depends on some important properties of the material, such as absorptivity, reflectivity, thermal conductivity, melting temperature, evaporation temperature, etc., among which the most important is the absorptivity.
Welding speed. The welding speed has a great influence on the penetration depth. Increasing the speed will make the penetration depth shallower, but too low a speed will cause excessive melting of the material and welding through the workpiece. Therefore, there is a suitable welding speed range for a certain material with a certain laser power and a certain thickness, and the maximum penetration depth can be obtained at the corresponding speed value. Figure 10-2 shows the relationship between the welding speed and penetration of 1018 steel.
Shielding gas. Inert gas is often used to protect the molten pool during laser welding. When the surface oxidation of some materials can be ignored, protection can also be ignored. However, for most applications, helium, argon, nitrogen and other gases are often used for protection to protect the workpiece from oxidation during welding.
Advantages of using laser welding in the automotive field:
The introduction of optical welding technology has injected new vitality into the automotive anti-collision beam connector, and it has become the golden choice of the manufacturing industry with its high efficiency, high quality and high strength.
Efficient production speed
Traditional welding methods may appear to be slow in the manufacture of anti-collision beam connectors, while laser welding technology has successfully increased the welding speed with its high energy density and high power. This means shorter production cycles and faster delivery speeds, providing automakers with greater flexibility and competitive advantages.
High-precision welding ensures structural consistency
The automotive anti-collision beam connector has extremely high requirements for welding accuracy, and laser welding technology achieves micron-level welding accuracy with its very precise focus. The high-precision welding process ensures the consistency of the anti-collision beam connector structure and improves the stability and safety of the overall body structure.
High-strength welds improve anti-collision performance
Anti-collision beam connectors need to play a strong protective role when a car collides, so the strength of the welds is particularly critical. Laser welding technology achieves high-strength welds, ensuring that the anti-collision beam connectors can firmly withstand the impact force when a collision occurs, and improving the overall anti-collision performance of the vehicle.
Promoter of lightweight design
The automotive manufacturing industry is gradually shifting to lightweight design to improve fuel efficiency and reduce exhaust emissions. Laser welding technology makes the structure of anti-collision beam connectors more compact by achieving high-precision welding, which helps to achieve lightweight design. Lightweight anti-collision beam connectors not only reduce the weight of the entire vehicle, but also improve the fuel economy of the vehicle.
Future trends in intelligent manufacturing
The development of laser welding technology helps intelligent manufacturing move towards the future. By introducing advanced CNC technology and automation systems, laser welding makes the large-scale production of anti-collision beam connectors more intelligent and efficient. Intelligent manufacturing not only improves production efficiency, but also reduces labor costs, creating better conditions for the sustainable development of the automotive manufacturing industry.
Advantages of laser welding:
The heat input is very small, the weld depth-to-width ratio is large, and the heat-affected zone is small, resulting in very small shrinkage and deformation of the workpiece, and no post-welding correction is required;
The weld strength is high, the welding speed is fast, the weld is narrow, and the surface condition is usually good, eliminating the need for post-welding cleaning and other work;
The welding consistency and stability are good, generally no filler metal and flux are added, and some dissimilar materials can be welded;
The beam is easy to control, and the welding positioning is accurate and easy to automate;
Non-contact processing, no need to pressurize the workpiece and perform surface treatment;
Small welding spots, high energy density, suitable for high-speed processing;
Short-time welding, no thermal impact on the outside world, and low thermal changes in the material itself Small shape and heat-affected zone, especially suitable for processing high melting point, high hardness, special materials;
No processing noise, no pollution to the environment;
Optical fiber can be used to achieve long-distance, difficult-to-reach parts, multi-channel simultaneous or time-sharing welding;
It is easy to change the laser output focal length and welding point position;
It is easy to be mounted on automatic machines and robot devices;
Compared with other welding process methods, the initial investment of laser welding is relatively large;
The assembly accuracy of the welded workpiece is high, and relatively speaking, the accuracy of beam control is also relatively high;
Due to the large spatter, the weld of penetration welding is rougher than brazing, but the strength is much stronger than ordinary spot welding.
Product recommend
JS-HWE LASER WELDING MACHINE
◆ High-precision accuracy for joining even small parts
◆ Low heat input for minimal distortion
◆ Non-contact welding — no degradation in the welding quality
◆ Higher yield, lower cost
JS-HWG LASER WELDING MACHINE
◆ high quality, high stability, high configuration, high security.
◆ with gas detection alarm, kinetic energy detection, machine minimize loss, to ensure that the machine life;
◆ Additional filters, anti-interference ability, maximize the stability of the machine.
Conclusion
The future of laser welding in the automotive industry looks promising, with ongoing research and development aimed at further enhancing its capabilities. Innovations such as hybrid laser welding, which combines laser welding with other welding techniques, are being explored to achieve even higher welding speeds and better joint properties. Additionally, advancements in laser sources, such as fiber lasers and diode lasers, are expected to improve the efficiency and versatility of laser welding systems.
JNJSINDUSTRY
China Leading Laser Welding Machine Manufacturer
We Follow Best Sevices
JNJSINDUSTRY focus on product quality and customer service
Attitude determines success or failure
- Technology Guidance
- Two-year warranty
- On-site training
- Maintenance guid