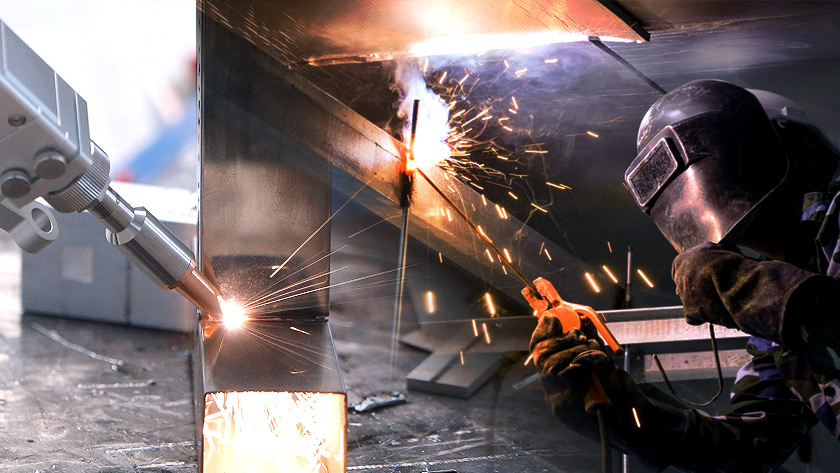
Laser welding has become an essential technology across multiple industries due to its precision, speed, and ability to produce strong, clean welds. This technology has proven to be particularly effective in industries where high-quality joints are crucial, such as in steel-wood furniture manufacturing, automobile production, stainless steel fabrication, lithium battery assembly, medical bed manufacturing, and general metal processing. Below, we will explore the applications of laser welding in these specific industries, highlighting how it has transformed manufacturing processes.
1. Steel-Wood Furniture Industry
1.1. Joint Strength and Aesthetics
In the steel-wood furniture industry, laser welding is used to join steel components to create sturdy, durable furniture pieces. The aesthetics of furniture are critical, and laser welding offers a clean, precise weld that requires minimal post-processing, ensuring a high-quality finish that enhances the overall appearance of the product.
- Frame Assembly: Steel frames are commonly used in modern furniture designs. Laser welding is employed to join steel components with minimal heat input, preventing warping or discoloration, and preserving the integrity of the wood elements that are often attached to these frames.
- Custom Designs: Laser welding allows for the creation of intricate, custom designs in steel furniture, enabling manufacturers to produce unique pieces that cater to specific customer preferences. The precision of laser welding ensures that even the most complex joints are strong and reliable.
1.2. Efficiency in Production
Laser welding enhances the efficiency of production in the steel-wood furniture industry by reducing welding time and improving the consistency of weld quality.
- Automated Welding Systems: The use of automated laser welding systems enables manufacturers to produce large quantities of furniture components with consistent quality, reducing production time and costs.
- Material Versatility: Laser welding can be applied to various steel grades and thicknesses, making it a versatile tool for different types of furniture. This versatility is particularly useful in the production of mixed-material furniture, where steel is combined with wood or other materials.
2. Automobile Manufacturing Industry
2.1. Body and Chassis Welding
Laser welding is extensively used in the automobile manufacturing industry, particularly for body and chassis assembly. The automotive sector demands high-strength, lightweight joints, and laser welding meets these requirements with precision.
- Body Panels: Laser welding is used to join thin steel sheets in car bodies, providing strong, continuous welds that improve the structural integrity of the vehicle while reducing weight.
- Roof and Door Assembly: Laser welding is employed in the assembly of car roofs and doors, where precision is critical to ensuring that the components fit together seamlessly and provide a tight seal.
2.2. Powertrain Components
The powertrain of a vehicle, which includes the engine, transmission, and drivetrain, requires robust joints that can withstand high stress and temperature. Laser welding is used to manufacture various powertrain components.
- Engine Blocks and Cylinder Heads: Laser welding is used to join components in the engine block and cylinder head, ensuring strong, leak-proof joints that can endure the high temperatures and pressures within an engine.
- Transmission Gears: Precision laser welding is used to join gears and other components in the transmission, contributing to the overall efficiency and durability of the vehicle.
2.3. Electric Vehicle Battery Assembly
With the growing demand for electric vehicles (EVs), laser welding has become essential in the assembly of lithium-ion batteries, which power these vehicles.
- Battery Cells: Laser welding is used to join battery cells with high precision, ensuring consistent electrical conductivity and reliability. The minimal heat input of laser welding prevents damage to sensitive battery components.
- Battery Modules: Laser welding is also employed to assemble battery modules and packs, providing strong, reliable connections that are crucial for the safety and performance of EVs.
3. Stainless Steel Industry
3.1. Precision Fabrication
Stainless steel is widely used in industries such as construction, food processing, and medical devices due to its corrosion resistance and strength. Laser welding is highly effective for joining stainless steel components.
- Thin-Walled Tubing: Laser welding is used to join thin-walled stainless steel tubes, ensuring precise, strong welds that are essential in applications like heat exchangers and medical instruments.
- Decorative Components: In architectural and decorative applications, laser welding is used to create clean, visually appealing joints that require minimal finishing, preserving the aesthetic quality of stainless steel products.
3.2. High-Strength Joints
Laser welding provides high-strength joints that are critical in applications where stainless steel components must withstand high stress or harsh environments.
- Pressure Vessels: In the manufacturing of pressure vessels and other industrial equipment, laser welding is used to join stainless steel components, ensuring they can withstand high pressures and temperatures.
- Food Processing Equipment: Stainless steel equipment used in food processing must be easy to clean and resistant to corrosion. Laser welding provides smooth, clean joints that meet these stringent hygiene requirements.
3.3. Medical Applications
The medical industry relies heavily on stainless steel due to its biocompatibility and resistance to corrosion. Laser welding is used to produce medical devices and implants with high precision.
- Surgical Instruments: Stainless steel surgical instruments, such as scalpels and forceps, are laser welded to ensure strong, precise joints that can withstand repeated sterilization.
- Implants: Laser welding is also used to manufacture stainless steel implants, such as bone plates and screws, where biocompatibility and strength are essential.
4. Lithium Battery Assembly Industry
4.1. Cell Manufacturing
Laser welding plays a crucial role in the manufacturing of lithium battery cells, particularly in the assembly of electrode tabs and connections.
- Electrode Tab Welding: Laser welding is used to join the electrode tabs to the cell casing with high precision, ensuring a secure connection that provides reliable electrical performance. The process minimizes heat input, reducing the risk of damage to the sensitive battery materials.
- Seam Welding: Laser welding is also used to create hermetic seals on battery cells, preventing the ingress of moisture and contaminants, which can degrade battery performance and safety.
4.2. Battery Module and Pack Assembly
In addition to cell manufacturing, laser welding is employed in the assembly of battery modules and packs, which are used in electric vehicles, consumer electronics, and energy storage systems.
- Module Connections: Laser welding is used to join the individual cells within a battery module, creating strong, reliable connections that are essential for the safe and efficient operation of the battery.
- Busbar Welding: The busbars, which connect the cells within a module, are also welded using lasers. This ensures a consistent electrical connection and minimizes resistance, contributing to the overall efficiency of the battery.
4.3. Heat Management
Effective heat management is critical in lithium battery assembly to prevent overheating, which can lead to battery failure or even fire. Laser welding offers precise control over heat input, making it ideal for this application.
- Thermal Control: The ability to control heat input during welding helps to minimize thermal stress on the battery components, ensuring their longevity and reliability.
- Cooling Plate Welding: Laser welding is used to join cooling plates to battery modules, ensuring efficient heat dissipation and maintaining the optimal operating temperature of the battery.
5. Medical Bed Manufacturing Industry
5.1. Frame Construction
In the medical bed manufacturing industry, laser welding is used to construct the frames of hospital beds, which must be strong, durable, and capable of supporting heavy loads.
- Steel Frames: Laser welding is employed to join steel components in medical bed frames, providing strong, reliable welds that ensure the bed’s stability and longevity.
- Adjustable Components: Medical beds often feature adjustable components, such as headrests and footrests. Laser welding provides the precision needed to join these components, ensuring smooth operation and durability.
5.2. Hygiene and Safety
Medical beds must meet strict hygiene and safety standards, and laser welding contributes to achieving these goals by producing smooth, clean joints that are easy to sterilize.
- Smooth Welds: Laser welding creates smooth, uniform joints that minimize the risk of bacteria buildup, making it easier to maintain the cleanliness of medical beds.
- Corrosion Resistance: The precision of laser welding ensures that the welds are corrosion-resistant, which is essential in the medical environment where equipment is frequently exposed to cleaning agents and disinfectants.
5.3. Lightweight Construction
The use of lightweight materials in medical beds is becoming increasingly common, and laser welding is ideal for joining these materials without compromising strength.
- Aluminum and Stainless Steel: Laser welding is used to join lightweight aluminum and stainless steel components, reducing the overall weight of the bed while maintaining its structural integrity.
- Portable Beds: For portable or foldable medical beds, laser welding provides the strong yet lightweight joints needed to ensure ease of transport and storage.
6. Metal Processing Industry
6.1. Precision Welding
The metal processing industry covers a wide range of applications, from heavy machinery to delicate components, and laser welding is employed for its precision and versatility.
- Thin Sheets and Foils: Laser welding is ideal for joining thin metal sheets and foils, providing precise, strong welds that are essential in industries like electronics and aerospace.
- Complex Geometries: In the production of components with complex geometries, laser welding allows for the precise joining of parts, ensuring the integrity and performance of the final product.
6.2. High-Speed Production
Laser welding is used in high-speed production environments where efficiency and consistency are crucial.
- Automated Welding: The use of automated laser welding systems in metal processing allows for the rapid production of components with consistent quality, reducing production time and costs.
- Batch Processing: Laser welding is also used in batch processing, where multiple components are welded simultaneously, further improving efficiency and throughput.
6.3. Surface Finish
The surface finish of welded components is critical in many metal processing applications, and laser welding provides a smooth, clean finish that often requires little to no post-processing.
- Aesthetic Components: For components where appearance is important, such as in consumer electronics or automotive interiors, laser welding provides a high-quality finish that enhances the visual appeal of the product.
- Reduced Post-Processing: The clean welds produced by laser welding minimize the need for post-processing, such as grinding or polishing, reducing manufacturing time and costs.
In summary, laser welding has become an indispensable technology in various industries, offering unmatched precision, strength, and efficiency in welding applications. Its ability to join a wide range of materials, from steel and stainless steel to aluminum and lithium-ion batteries, makes it a versatile tool that continues to drive innovation and quality in manufacturing processes across the globe.